DR Plans for Chemical Explosions
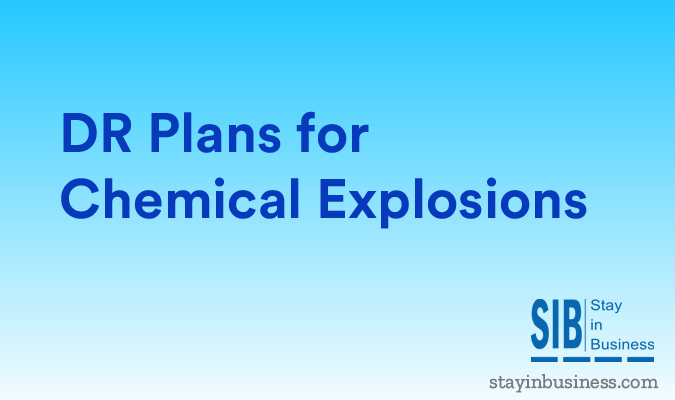
In the world of disaster recovery, accidents caused by chemicals are a story we have come across many times before. A massive explosion at a manufacturing facility – in this case, a chemical plant at Yancheng – claimed the lives of 64 people while more than 640 people suffered severe injuries. The damage to the surroundings and flora in the locality was also significant. Thousands of workers in and around the area had to evacuate. The share prices of dye companies registered record highs due to the expected shortages. One can only hope that the impact of the explosion is minimal on businesses that depend on the dyes and chemicals, and that they at least have alternate supplier options.
In another incident, the City of Deer Park in Texas, where the Intercontinental Terminals Company is located, was hit with an explosion. The state’s southeast was covered in a cloud of smoke for days on end owing to chemical fires. Many are even worried about the dangerously high content of benzene and other volatile organic compounds. The situation was critical enough for a shelter-in-place order to be issued in two nearby towns, Galena Park and Deer Park. The fire raged nonstop for four days. Seven tanks that were stocked up with highly flammable substances that are used to make gasoline such as naptha, xylene and pyrolysis gasoline, also known as Pygas, provided the fires with a generous supply of fuel.
Such situations are made worse by insufficient and inadequate business continuity and disaster recovery plans. Even customers don’t have plans in place when a vendor’s supplies are interrupted. The need is a high degree of vendor involvement in the business continuity and disaster recovery plans of suppliers. Segments that are critical to their business must be closely reviewed. And, in order to have a clear picture of all the risks involved, customers must also have visibility into the operations of the next level of sub contractors.
It is not uncommon for first responders to confront such situations without even knowing what chemicals they have to deal with in the facilities. Even basic requirements such as access to the Material Safety Data Sheet (MSDS) – a critical disaster recovery component in such situations – are frequently not available.
Get acquainted with your neighborhood. Are there chemical or gas companies or gas storage stations nearby? Is there a railway line near your facility that freight trains carrying chemicals, oil or gas might use? How will your company stay protected and stay in business? Where will your disaster recovery plans be located? How will you get in touch with your staff and stakeholders?
Stay In Business is a cloud based platform that can elevate your organization’s business continuity and disaster recovery planning to the highest level of resiliency. Now you can stay prepared for any event. When crisis strikes your disaster recovery plans that are in the cloud based platform are readily accessible by staff members and can be instantly deployed into action.
Now, that’s how you stay in business!
Categories: Business Continuity, Crisis Management, Disaster Recovery Planning, DR Plans, Employee Safety, Fire, Health, Safety