Semi conductor Shortage and its impact on global Supply chains
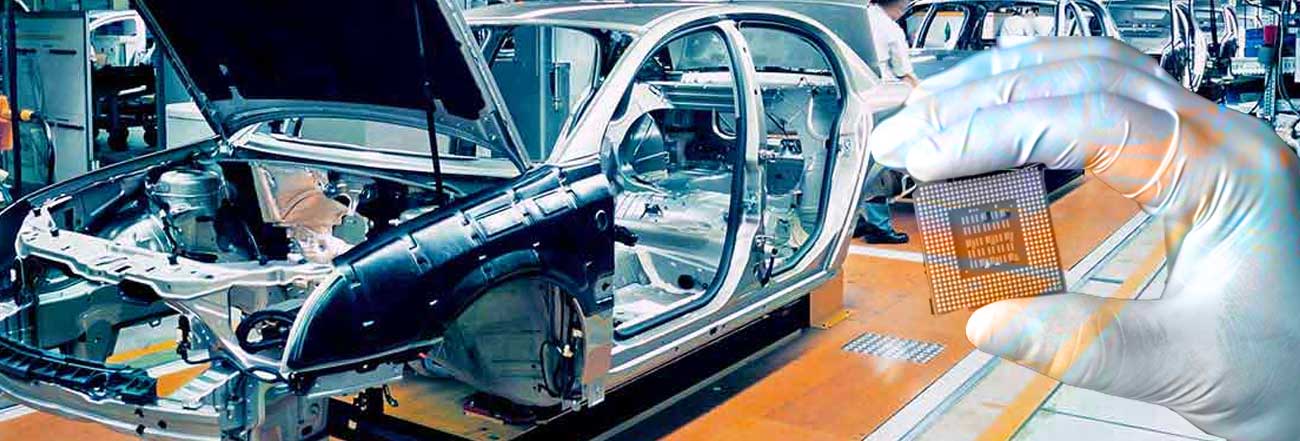
– Déjà vu 10 years later.
The slow return to normal in the auto industry just got even more lethargic as almost all car manufacturers have had to cut back on production.
Globally, automobile manufacturing is witnessing a prolonged lull. Operations and employee morale have hit an all time low. Car dealership companies are finding it nearly impossible to find new customers.
The crisis was caused by a dearth in supply of semiconductors that manage the automobile’s fuel injection calibration, infotainment, cruise control and other functions.
An acute shortage of these chips forced General Motors to shut down one of their facilities in Kansas City earlier this year and are yet to resume operations there. Mercedes-Benz is being extremely cautious by prioritizing the use of their available semiconductor stock strictly for their higher end models at the expense of their less expensive ones. Shortage of tire pressure monitoring chips has obliged Porsche to tentatively delay delivery by three months. Others such as Peugeot that recently merged with Stellantis are making do with makeshift arrangements such as using digital speedometers instead of their analog counterparts wherever possible.
An Ill Timed Chip Shortage Crisis
The semiconductor shortage has hit the automobile industry just when things were beginning to look up. Car dealers were experiencing a sudden spike in bookings after an uneventful 2020 – a year during which many prospective customers had been patiently saving up to make a car purchase this year. Road travel was gaining popularity as a very feasible alternative to air travel and automobile companies were looking to cash in on this rise in demand to recover their previous year’s losses.
Leadership team executives from Daimler commented that the slump in car production was caused almost entirely by the sudden shortfall of semiconductor supply.
How the Automobile Industry is Adapting to the Chip Shortage Crisis
Companies are being forced to generate more revenue with less production. The cars least impacted by this crisis across all organizations in the industry are the models with the lowest production costs and yet the highest margins. These models are invariably the ones that get manufactured for which the sparingly available semiconductor chips are made available.
Some manufacturers are also considering the option of releasing cars into the market but with only the features that don’t involve the use of semiconductors. For instance, one of the Porsche models allows passengers to adapt their seats in multiple manners based on their comfort. Porsche now won’t be able to release this car with this feature because of the semiconductor shortage.
The Automobile Industry is Not a Lucrative Market for Semiconductor Companies
Globally, the automobile industry is being sidelined by their semiconductor suppliers in favor of more rewarding customers such as smartphone, video game console and other consumer electronics companies.
Despite present day cars being heavily reliant on chips – a car might use thousands of chips – the automobile industry is not a high priority target segment for semiconductor suppliers. As per reports, even multinational semiconductor manufacturing companies with an exhaustive catalogue of different types of chips receive only marginal revenues from their customers in the automobile industry.
This is because the big business for semiconductor suppliers comes from the smartphone industry that contributes nearly fifty percent of their revenues. Smartphone companies have an almost unsurpassable competitive edge over their car manufacturing counterparts by the sheer volume of business and profit margins they offer to semiconductor suppliers. Even a couple of years ago, before the outbreak of the pandemic, the manufacture of smartphone units outnumbered those of automobiles by many hundreds of millions, even billions.
Dwindling Numbers of Automobile Production
The first quarter of 2021 saw automobile production fall short by over a million vehicles primarily because of a lack of semiconductors. The situation has become serious enough that the governments of leading nations have gotten involved.
Germany’s finance ministry has been persistently negotiating with Taiwan for emergency supplies of semiconductors to give their globally renowned automobile industry a much needed stimulus. Most of the car manufacturing companies in the country are in dire need of chips to keep their assembly lines moving.
Factors Contributing to the Shortage of Semiconductors
The semiconductor industry consists of a few major players, each with sizeable market shares, on whom the entire automobile industry is dependent. Such a scenario makes car manufacturing companies extremely susceptible to any fluctuation in the supply of semiconductors. An important Japanese manufacturer of semiconductors that manage brakes, power steering, airbag mechanisms and other tasks suffered a major fire at one of their facilities which disrupted supply to many automobile companies.
Inclement weather has also been detrimental to semiconductor production. Many facilities in Texas had to close operations due to heavy snowstorms. Taiwan on the other hand has been experiencing extremely dry weather and insufficient pure water – a crucial component in chip manufacturing – and as a result, hasn’t been able to produce chips at full throttle.
The car industry has had very little to cheer about since the turn of the century. Sales numbers have been witnessing a steady decline over the last two decades with narrow profit margins. The transition to electric motors with rechargeable batteries mean that many car companies might even go out of business.
Semiconductor Supply Chain Environment – Current Scenario
Supply chain management experts strongly advice against investing in chip manufacturing without substantial subsidies and support from the government.
The US Government has already made a tangible commitment to address the issue and is in the process of provisioning $50 billion to fortify the chip manufacturing industry’s production capabilities. However, constructing new chip manufacturing facilities with state of the art equipment would take time and won’t resolve the current issue of insufficient chips that is hampering production today.
Chip manufacturing companies are already looking at alternate locations for their new facilities if government assistance doesn’t cushion the financial impact of investing in new facilities. China figures prominently in this list of alternate locations and is also the world’s largest consumer of automobiles. Besides, its economy has been developing consistently over the years.
When Will the Automobile Chip Crisis End?
There is no foreseeable end to the current chip shortage. Some supply chain experts are even speculating if the chip manfacturing companies’ woes are intentionally unfounded merely to coax the government into providing financial assistance and the crisis might come to an end in less than a month.
Other advisers to the automobile industry however project a slower recovery that may span an entire year. Representatives from Renault suggested that given the lack of clarity on what is a constantly evolving situation, it is near impossible to foresee a tangible timeframe within which the chip crisis would be brought to an end.
Ad Hoc Solutions for the Automobile Industry
Meanwhile, car companies are trying to soften the blow with ad hoc solutions.
Daimler
Daimler’s Mercedes is reserving its sparsely available chip stock for its most expensive models, for example the EQS which was introduced recently in the market and is priced at approximately $100,000.
This strategy of prioritizing chips for their more expensive models forced the company to close operations for the time being in facilities that manufacture more affordable models. Tens of thousands of employees at these facilities have been granted temporary leave of absence till the end of April. The government for their part are extending support to these workers in the form of short work pay.
Volkswagen
Volkswagen has followed suit with a similar approach. Operations have been stalled at their German facilities that produce sedans and cars that involve internal combustion. One of their Mexican factories that export SUVs to the USA has also been temporarily shut down. However, one Volkswagen production center in Zwickau, Germany, that specializes in electric sedans and SUVs, continues operating in order to stay competitive.
General Motors
Multiple General Motors factories haven’t been operating throughout 2021. Some of their factories have been churning out cars without electrical components and putting their delivery on hold until the supply of these parts resume. Numerous Ford Motor factories also wouldn’t be operating for a prolonged period of time due to insufficient semiconductor stocks.
Supply Chain Disruptions in the Car Industry
Supply chain disruptions are not uncommon in the automobile sector. Even environmental hazards can short circuit the flow of goods as was the case once in Puerto Rico when a hurricane forced a factory to close. This factory was the sole provider of a specialized type of coating without which specific auto electronics cannot be manufactured.
The supply of automobile parts consists of a multilayered network with numerous hierarchical and sub-hierarchical chains of command among suppliers. This makes it very difficult for automobile companies to track the thousands of components they source for each of their car units.
Survival in the automobile supply chain terrain is closely tied to dealing in large volumes. Smaller chip manufacturing companies can’t scale up their operations as it would imply greater overhead costs. And so they lose out to competition from the bigger companies. This means that almost all the car companies are slavishly dependent on a few privileged chip manufacturers who have a monopoly over the semiconductor market. This is especially true in the case of specialized components.
Conclusion
It is important that large manufacturers understand their supply chain better. Car manufacturers depend on their Tier 1 Suppliers who in turn depend on Tier 2 suppliers and so on. Very few manufacturers review a Business Continuity Plan of their suppliers. During vendor qualifications all they ask is a question, Do you have a Business Continuity Plan?’ and vendors check them off. They do not check to see if there is a supply chain redundancy. Many Business Continuity plans are old and out of date. This scenario was played out before during the Fukushima earthquake when a Mitsubishi Gas Chemical factory in Fukushima was damaged by the resulting tsunami and there was a shortage of bismaleimide triazine, BT, a resin used in the packaging if comput5er chips and two Japanese companies controlled 60% of the world’s supply of bismaleimide triazine, BT. Stayinbusiness.com can help conduct such a study to highlight the risks in the supply chain, and the on-line platform can provide an insight into the dangers posed by such lack of resiliency.
Categories: Crisis Management, Manufacturing, Supply Chain